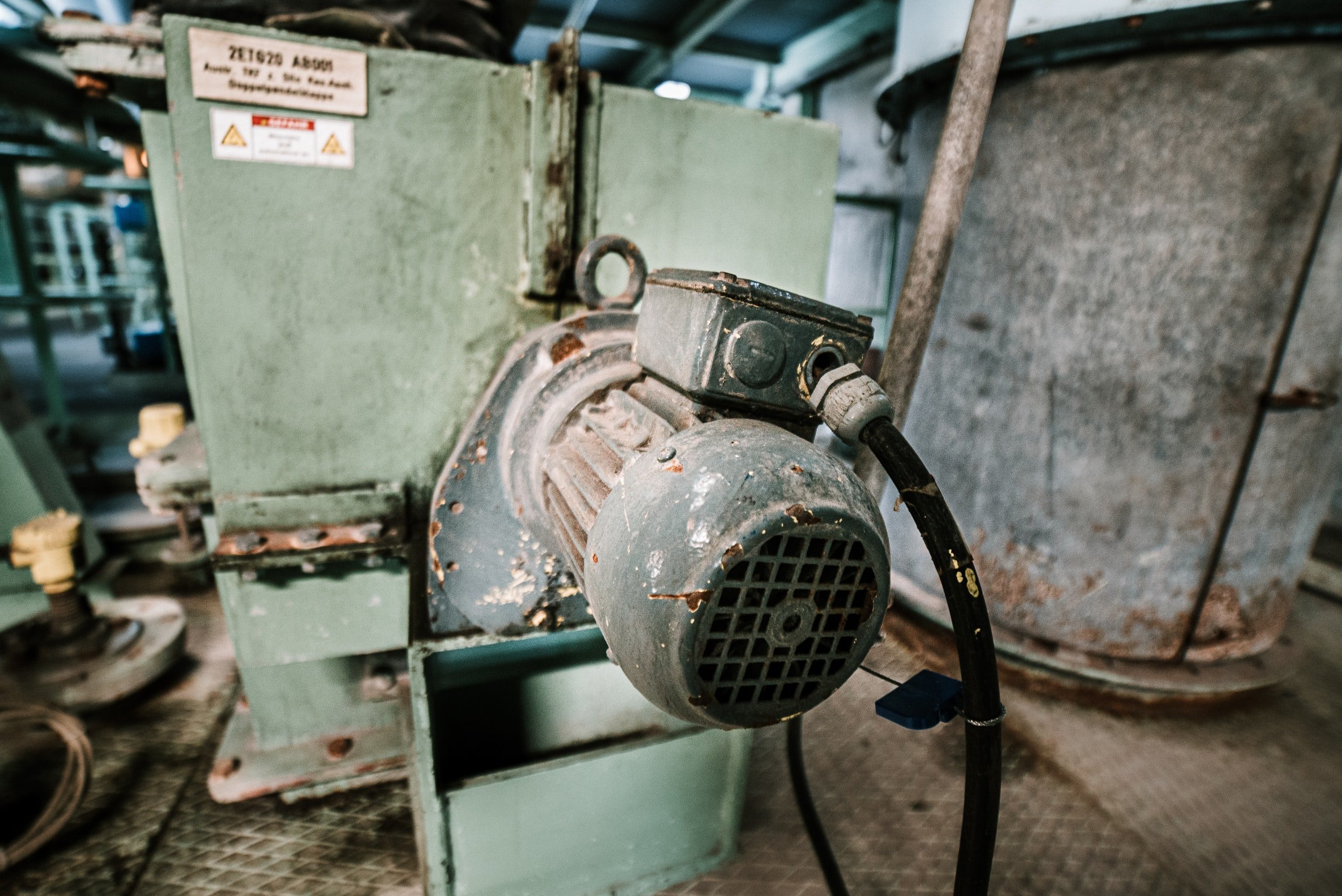
WHY VIBRATION ANALYSIS?
DECREASE DOWNTIME AND INCREASE PROFITABILITY
Traditional maintenance methods are preventive - Components are replaced according to a fixed schedule whether worn or not. Traditional maintenance methods are also reactive, repairing components only after they have broken down.
Neither of these methods is ideal, although both are very common throughout the heavy industry sector, and both tend to sustain much higher costs than methods that use vibration analysis.
EARLY DETECTION OF MECHANICAL FATIGUE AND BREAKDOWN
All rotating equipment vibrates to some degree, but as older bearings and components reach the end of their product life, the vibration gets more and more intense and in distinct ways.
Continuous monitoring of equipment allows these signs of wear and damage to be identified before the damage becomes an expensive problem.
ALERT IS PROACTIVE
ALERT can help maintenance departments using reactive maintenance practices (fixing problems as they present themselves or when machinery is broken down). By using ALERT Services operations can move towards a proactive way of managing maintenance.
ALERT visits plants on a scheduled basis, collecting vibration data and performing detailed analysis of each machine. A report is then issued including suggested actions craftsmen can respond to. ALERT’s services are priced so that even the smallest plants can afford the transition from Reactive to Proactive Maintenance.
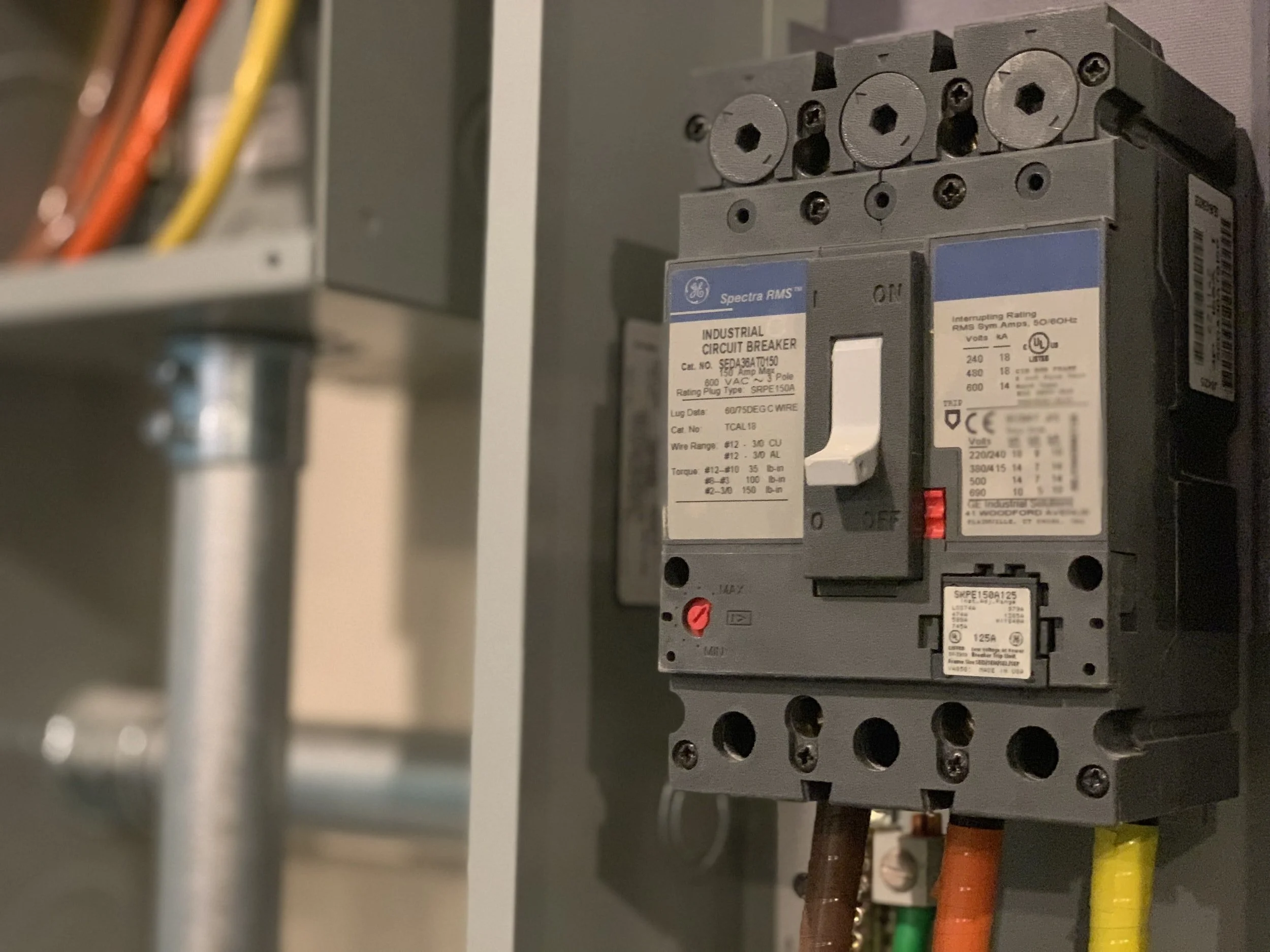
Infrared Thermography
ALERT uses infrared inspection to visualize, measure, document thermal performance and to identify thermal problems before they can cause costly damage or downtime. Typical faults identified using infrared thermography imaging include:
Mechanical Defects - verify machinery wear causing friction-related heat
Electrical Systems - accurately diagnose irregularities in electrical system
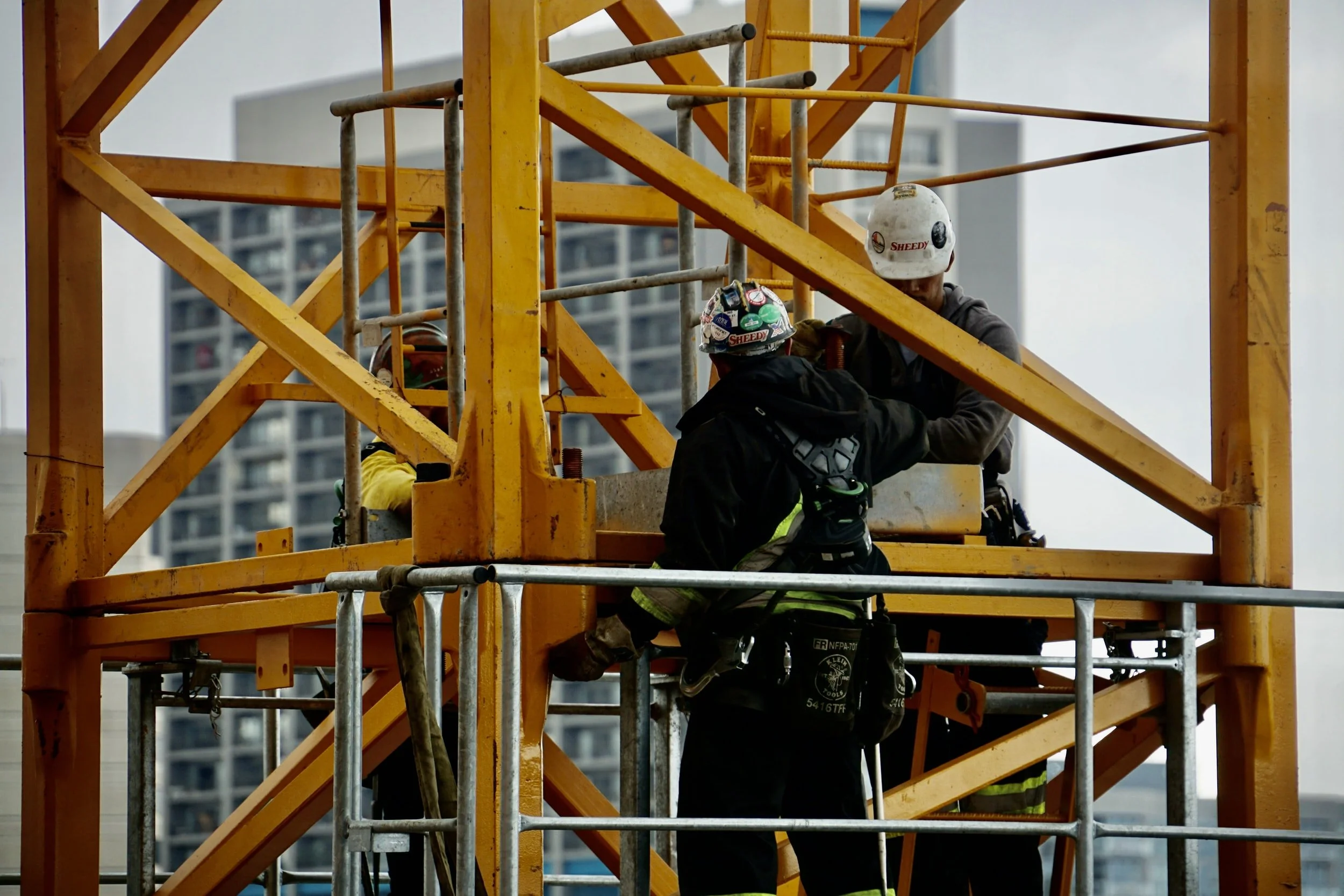
Maintenance Detective Training
ALERT offers this crash course on equipment realiability to teach you how to move from a reactive to a proactive maintenance culture. This 8 hour course will train your front line maintenance personnel how to identify and correct equipment issues. This is a classroom course that engages your maintenance personnel with the goal of reducing downtime and equipment cost by finding and or eliminating equipment issues.
Understanding Vibration for craftsmen
Stroboscope - understanding machine movement
Infrared Thermography
Root Cause Failure Analysis for the front line personnel
How and why to move from a reactive to a proactive maintenance culture